Career Opportunities
As a team member of the leading industrial oven and furnace manufacturer serving a variety of industries, you can contribute to large-scale thermal processing equipment projects from conception through to manufacturing. Each role within ITS plays an important role in providing exceptional customer service, and excellent products. Our employees are what make ITS a leading manufacturer in multiple industries.
International Thermal Systems is committed to recruiting and hiring qualified individuals in all job titles without regard to race, color, sex, age, national origin, religion, disability, genetic information, sexual orientation, veteran status, or other classes protected by applicable law. International Thermal Systems is an Equal Opportunity Employer.
International Thermal Systems is the Place to Work
ITS has manufactured heat processing equipment for over 50 years and is committed to growth by adding value to the industry and by investing in our employees. ITS employs approximately 100 people between our corporate manufacturing facility in Milwaukee, WI and our manufacturing facility in Shanghai, China.
Our team at ITS is made out of talented, hardworking individuals. Our team ranges from Administrative positions, Customer Support, Engineering, Sales, Manufacturing and more. We pride ourselves on providing an excellent work environment for our employees and cultivating a culture that supports our employees in both their roles and in their careers.
We are also proud to offer a complete benefits package that includes insurance, 401K, training and wellness.
Find a position that’s right for you and join our team today!
Check Out our Employee Benefits and Perks
Health and Dental Plans
- Medical and Dental Insurance Coverage
- Single, Employee/Spouse, Employee/Children and Family Plans are Available
- Employees working 32 hours per week are eligible for coverage the first day of the month following 60 days of continued service
- Wellness Incentives Available
- ITS pays 80% of premium, employee’s portion is pre-tax
401(k) Plan
- Managed by Associated Bank
- ITS will match 50% of the first 6% of employee contributions
- Both Pre-Tax and Roth 401(k) options available
- Available to all employees over the age of nineteen and after 60 days of continuous service
Health Savings Account (HSA)
- Health Savings Account with Company Match Available
Tuition Reimbursement
- Tuition reimbursement for approved courses and degree programs
- Full time employees are eligible after completing six months of employment
Career Development
- Career development plans that allow for employees to work with their managers to help create their career at ITS
- Tiered positions at ITS allow for individuals to visualize a career plan and allows for continued career growth
Insurance & Disability
- Basic Life Insurance paid by ITS
- Accidental Death and Dismemberment Insurance – Paid by ITS
- Short Term Disability – 100% Paid by ITS
- Long Term Disability – Voluntary
- Employees have the opportunity to purchase additional life insurance at group rates
Other Benefits ITS is Proud to Offer
- Vacation Pay
- 10 Paid Holidays + Floating Holiday
- Direct Deposit
- Employee Referral Bonus
- Annual Christmas Party
- Company Outings
- Bereavement Pay
- Prescription Safety Glasses
- Safety Shoe Allowance
- Employee Assistance Program
- Purchasable Vacation Time
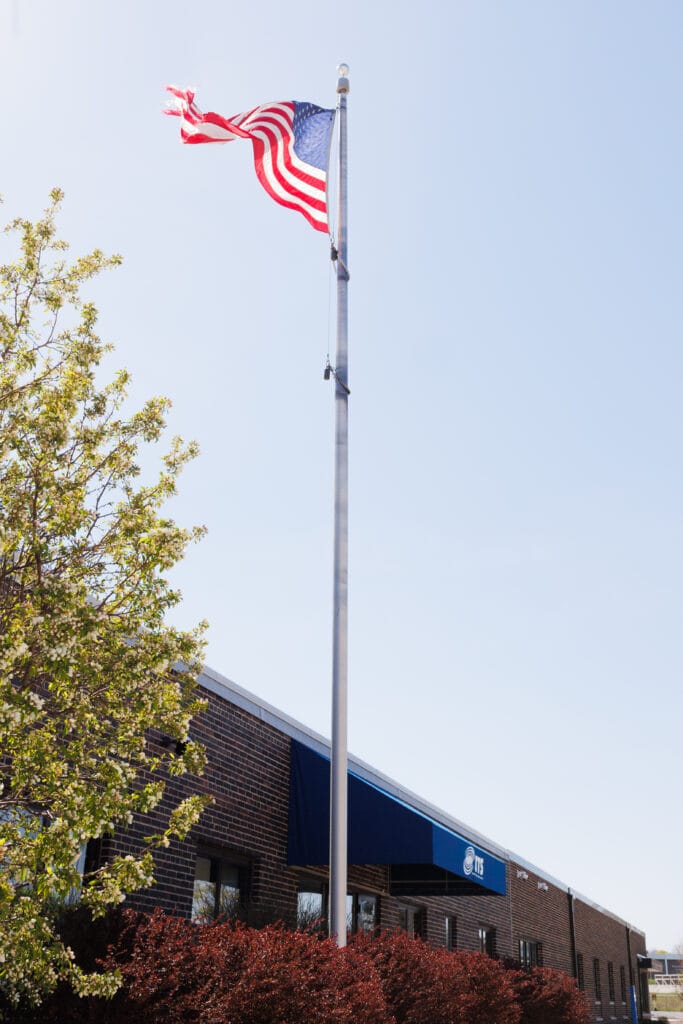
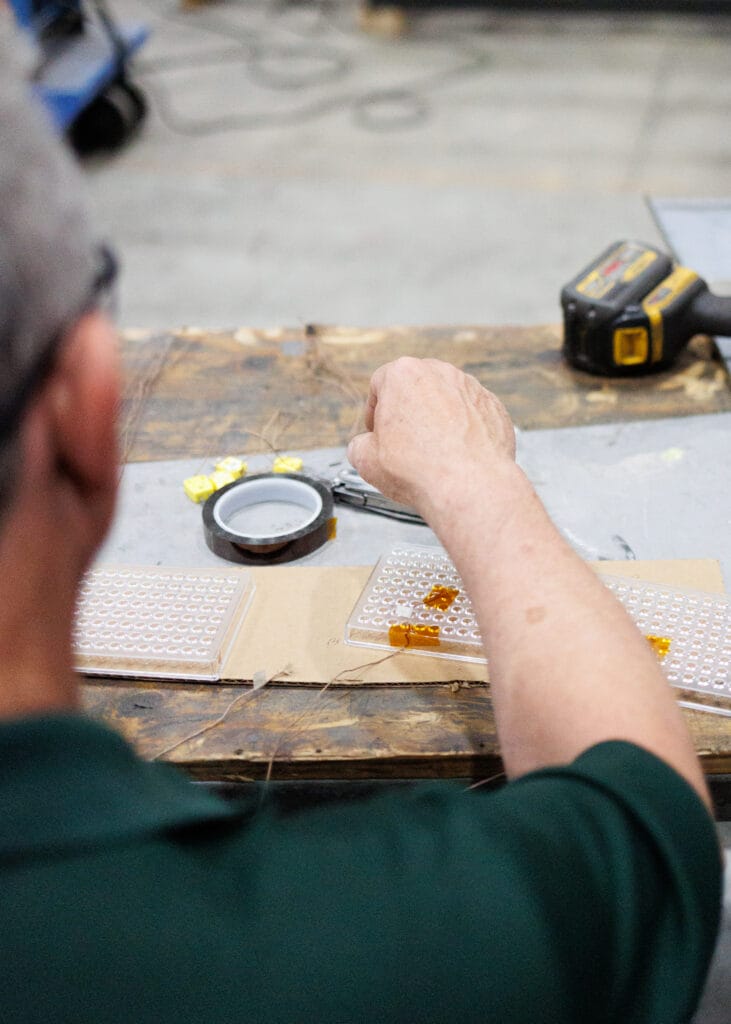
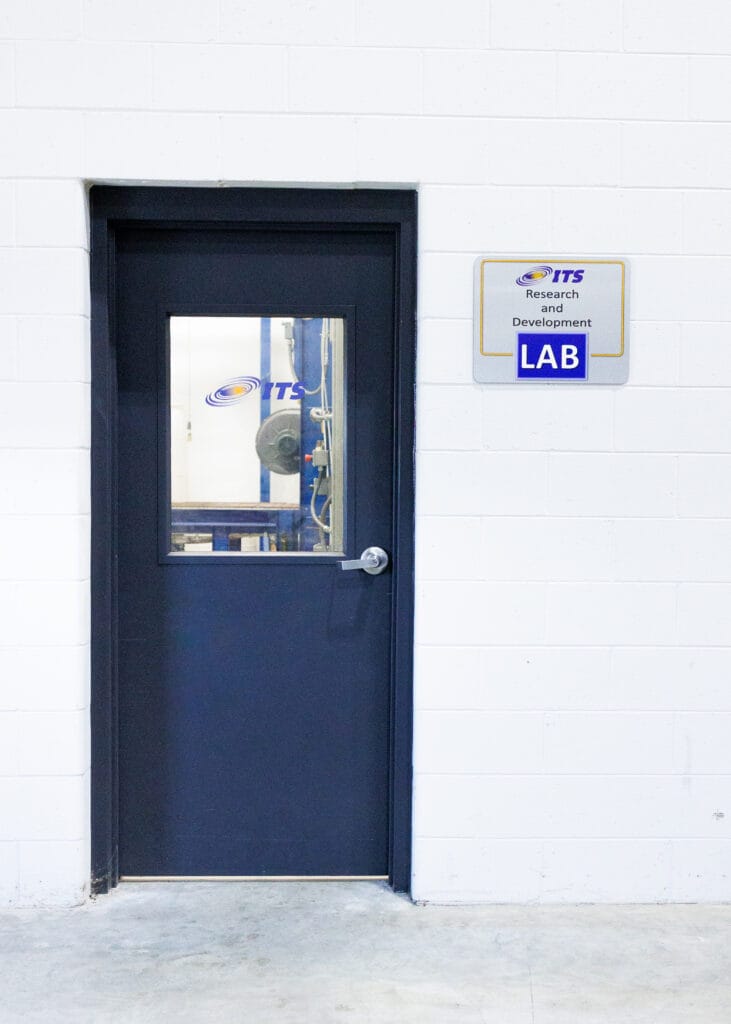
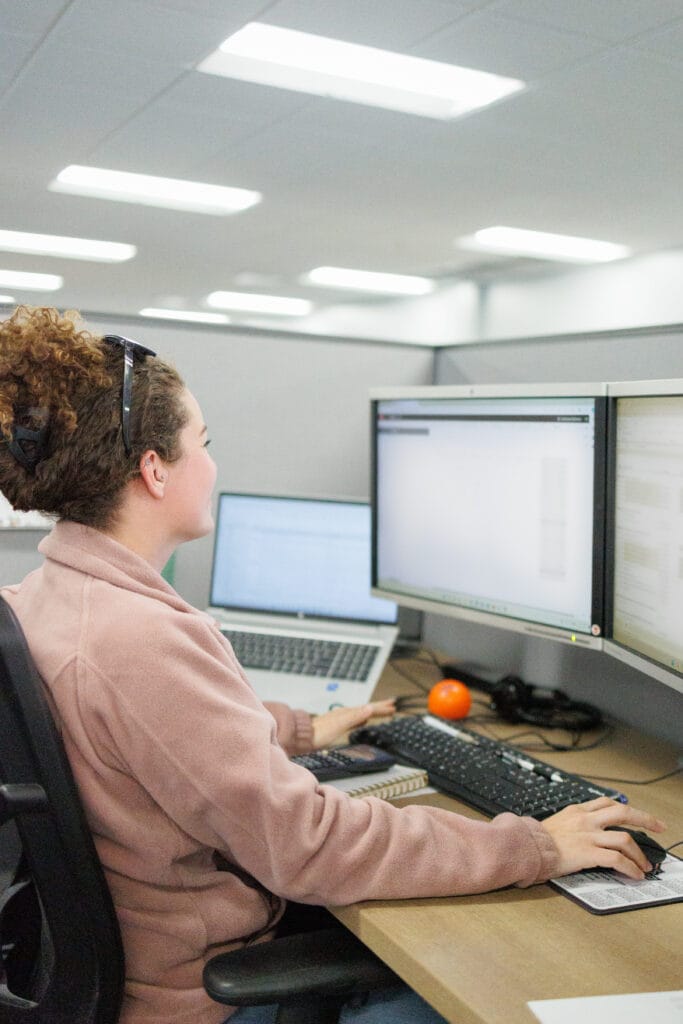
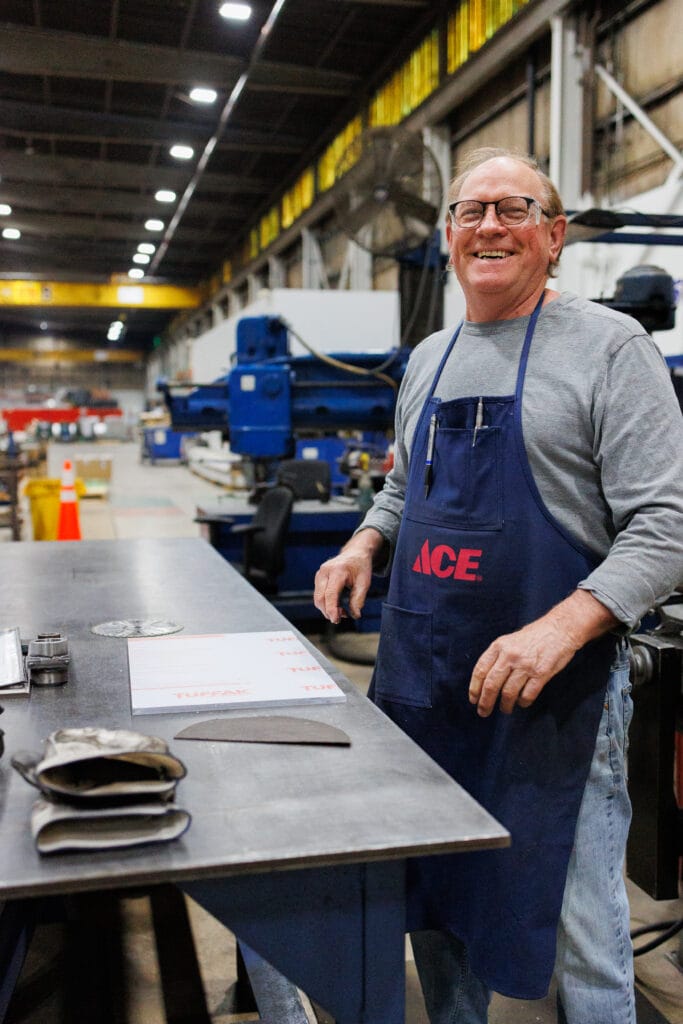