Visit ITS at CAMX 2019 in Anaheim, September 23-26
We are looking forward to attending CAMX next week in Anaheim. CAMX is dedicated to the composite curing industry and provides the opportunity to meet with companies that are leading the industry in technological advancements in equipment and processes. ITS will be presenting our complete out of autoclave solutions with our TruTemp batch ovens.
Visit ITS at CAMX in Booth K22
Learn more about composite curing and out of autoclave processing:
Out-Of Autoclave (OOA) Composite Curing Tutorial
Composite Curing History
Over the past few years the use of composites has increased dramatically in various products we see every day. From Sporting goods to Oil and Gas, Automotive and Aerospace parts, composites and advanced composites are becoming much more common than you would think.
As far back as 1941 Ford created a “Soybean car” prototype vehicle that featured panels that were made “plastic” and included a variety of materials – including jute, soybean and hemp and held together with a phenolic resin. In the 1950’s Boeing started incorporating fiberglass composites in passenger jet aircraft and currently the 787 Boeing Dreamliner is comprised of approximately 50% advanced composites by weight. The Airbus A350 AXB also utilizes more than 50% advanced composites by weight. Some specific examples of these types of parts include: landing gear doors, radomes, fuselage and wing sections.
Composites 101
These composites are comprised primarily of thermoplastics and thermoset prepreg sheets. These “prepreg”sheets are woven materials that have not yet been impregnated with a resin. Normally, this process will usually require application of resin and the precise monitoring of a variety of steps. These prepreg laminates are oriented in a specific direction during “lay-up” until the desired part thickness is achieved. In between each layer, epoxy resins are applied to the laminates which will later provide stiffness and support to the part once it is processed. Care must be taken to choose the appropriate resin for the application. Another important component of the lay-up and curing process is the elimination of voids in between each laminate. Variables such as viscosity and temperature can have an impact on the elimination of voids during processing. Traditionally, these parts were introduced into autoclaves under vacuum.
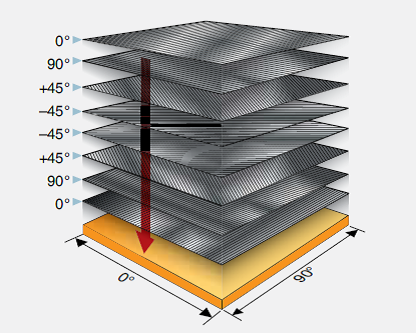
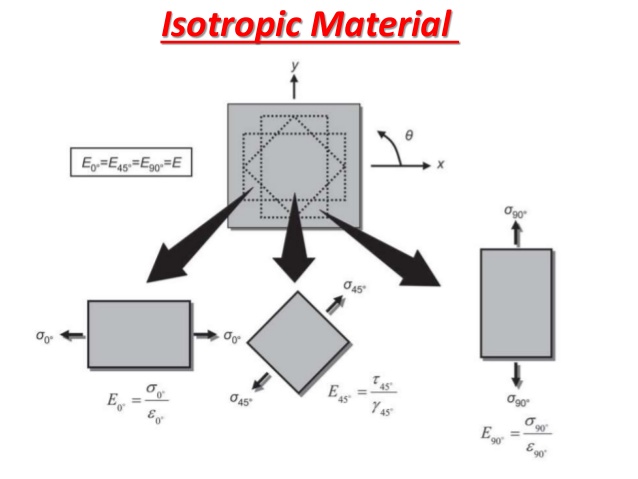
Evolution of Processes and challenges
Within the past decade or so a different processing method has been gaining in popularity; Out Of Autoclave (OOA) vacuum curing and Vacuum Bag Only (VBO) curing. These methods can offer some benefits over the autoclave process based lower initial capital and long term operating costs which are much lower than autoclaves. In addition, there is greater flexibility in the sizes of parts that may be processed. However, one drawback in OOA processing may be longer cycle times needed to reduce voids in the part. The removal of voids is extremely important to maintain the structural rigidity of the finished workpiece. The current standard is <1%. Voids > 1% can greatly affect the quality of the workpiece. In Aerospace applications this is critical. This goal can be achieved with OOA curing however, care must be taken in the proper lay-up of the part since autoclaves work under higher pressure. Voids occur due to the imperfections found in reinforced composite materials and occur from the trapping of air or volatiles generated during the curing process. These voids are eliminated during the vacuum process and the extraction of air and volatiles from the workpiece.

Differences in Autoclave and OOA Processes
The main difference between a typical Autoclave and OOA and VBO batch oven is how the vacuum is generated. Where in an autoclave the entire chamber is under vacuum, in a batch oven the workpiece is under vacuum since it is contained in the vacuum bag.
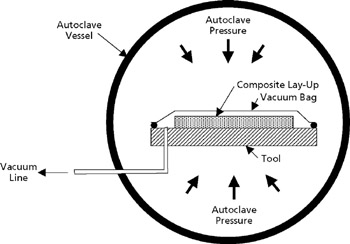
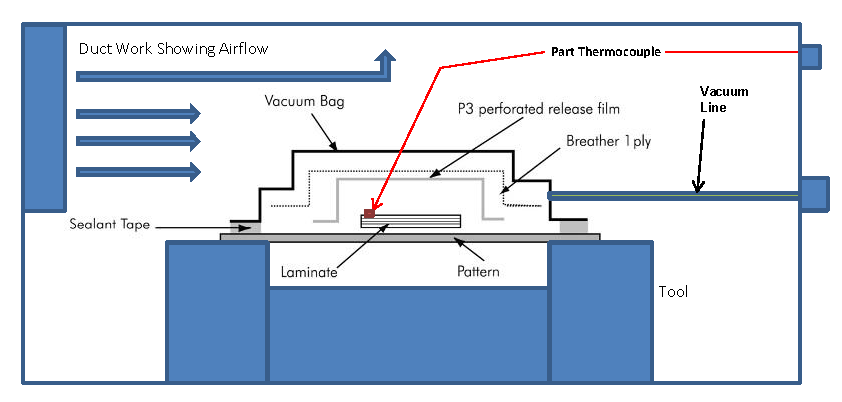
As we have discussed, in order to achieve the desired results in any of these methods, especially in Advanced Composites applications, it is important to follow the appropriate protocols and guidelines when preparing a workpiece for processing.
How composites are processed using ovens instead of an Autoclave
Advanced Composites cure ovens differ significantly from other batch ovens due to the additional requirements of the process. These composite cure OOA batch ovens will incorporate the following additional features:
- Combination airflow –airflow is an important feature to ensure proper curing of the part
- Impinging features to increase airflow onto the workpiece, especially for complex geometry parts. These features can include nozzles to direct airflow to a specific area of the workpiece
- Thermocouple ports – to monitor the part temperature as well as the process temperature inside the oven
- Vacuum ports- to connect the workpiece to the vacuum system
- Vacuum system-to subject the workpiece to the desired level of vacuum (typically 25”Hg and a loss of <1” Hg/hour)
- Auxiliary cooling-to aid in controlled cooling of the part. The addition of motorized dampers that are actuated at a desired temperature set point.
- Ability to meet AMS 2750 E and other aerospace requirements
- Thermocouple accuracy
- Traceability
- Number of workpieces processed
- Ability to meet system accuracy tests (SAT)
- Ability to meet temperature uniformity surveys (TUS)
- Tight temperature uniformity +/- 5°F
In addition, it is critical to monitor the cure process and these ovens will incorporate advanced control systems to keep track of:
- Oven temperature (ramp-up, dwell and cool-down)
- Part Temperature
- Ability to monitor the entire curing process
- Ability to generate process data
- Ability to archive process data
- Multiple recipes to accommodate different parts
- Ability to monitor and control vacuum to ensure void free parts
After undergoing the appropriate steps in the lay-up process the workpiece and tool are usually placed on a cart and introduced into a “cold” oven. Recipes will be dependent on a number of parameters. These parameters may include the type of resin being utilized, the thickness of the workpiece, weight of the workpiece, weight of the tool, cure temperature of the resin, the time required to cure the resin etc. All of the variables mentioned above will influence the ramp-up, dwell and cool down of the workpiece in the oven. Once the process is established, the operator can program a recipe into the controller to achieve the desired result and obtain a good part.
Future Outlook
OOA vacuum curing will likely not replace autoclave processes especially when the initial investment for an autoclave has already been made however; there are many existing and new applications where OOA vacuum curing may offer benefits over autoclave processing. As the OOA process matures we are very likely to see an increase in the use more cost effective and flexible technology.
Written by: Ernie Serrano
For more information on composite curing ovens and the capabilities of ITS, contact International Thermal Systems @
sales@itsllcusa.com
414.672.7700
Download this Out of Autoclave Composite Curing Oven Tutorial